How Long Do Concrete Coatings Last? Lifespan and Durability Guide
Concrete coatings protect and enhance surfaces in residential, commercial, and industrial settings. Understanding their longevity, maintenance requirements, and durability factors helps property owners make informed decisions about epoxy, polyurethane, and polyurea applications for basement floors, garage surfaces, driveways, patios, decks, and warehouse environments where superior waterproofing and aesthetics are essential.
Key Factors Affecting Coating Lifespan
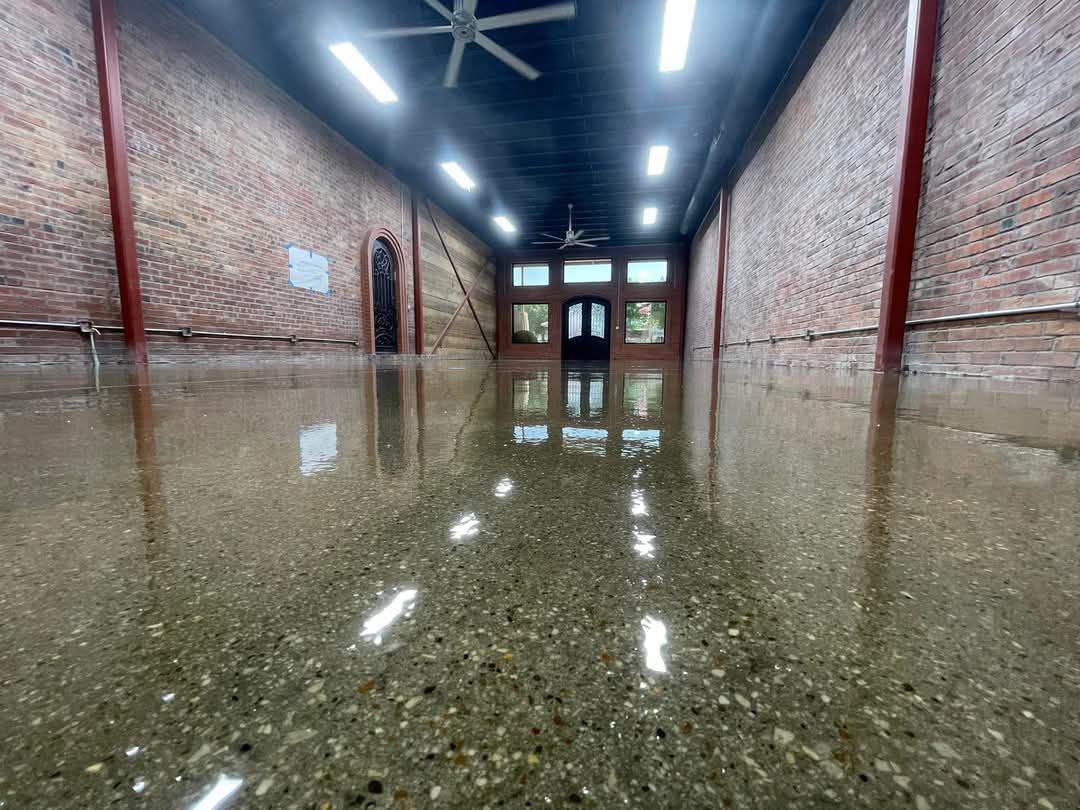
Understanding the critical elements that determine how long your concrete coating will last is essential for maximizing your investment and ensuring optimal performance across different applications.
Coating Type and Chemical Composition
The chemical formulation directly impacts resistance to abrasion, chemicals, and weather conditions. Epoxy coatings provide hard, glossy finishes with strong adhesion but may degrade under UV exposure and sunlight. These coating systems excel in basement floors and garage applications where oil and grease resistance matter. Polyurea coatings cure rapidly and resist stress from heavy equipment and heat, making them ideal for warehouse floors. Polyurethane coatings combine flexibility with excellent impact resistance, perfect for decorative concrete applications where aesthetics and durability are equally important. Latex-based systems offer economical alternatives but typically have shorter life expectancies.
Surface Preparation and Adhesion
Proper surface preparation ensures successful coating adhesion and longevity. Concrete surfaces must be thoroughly cleaned through pressure washing, etched to remove contaminants like oil, grease, dirt, dust, and soil, then primed for optimal bonding. Well-prepared surfaces provide uniformity and help distribute stress from tire traffic and heavy equipment, reducing crack risks while improving overall life expectancy and waterproofing effectiveness.
Environmental Conditions and Climate Impact
Harsh environmental exposure significantly impacts coating lifespan and durability. UV radiation from sunlight, extreme temperatures, humidity fluctuations, and climate variations accelerate paint and coating degradation. Moisture infiltration causes deterioration when waterproofing is inadequate, while pollutants, soil contamination, and temperature cycling contribute to chemical reactions that weaken epoxy and polyurethane systems over time.
Average Lifespan by Coating Type
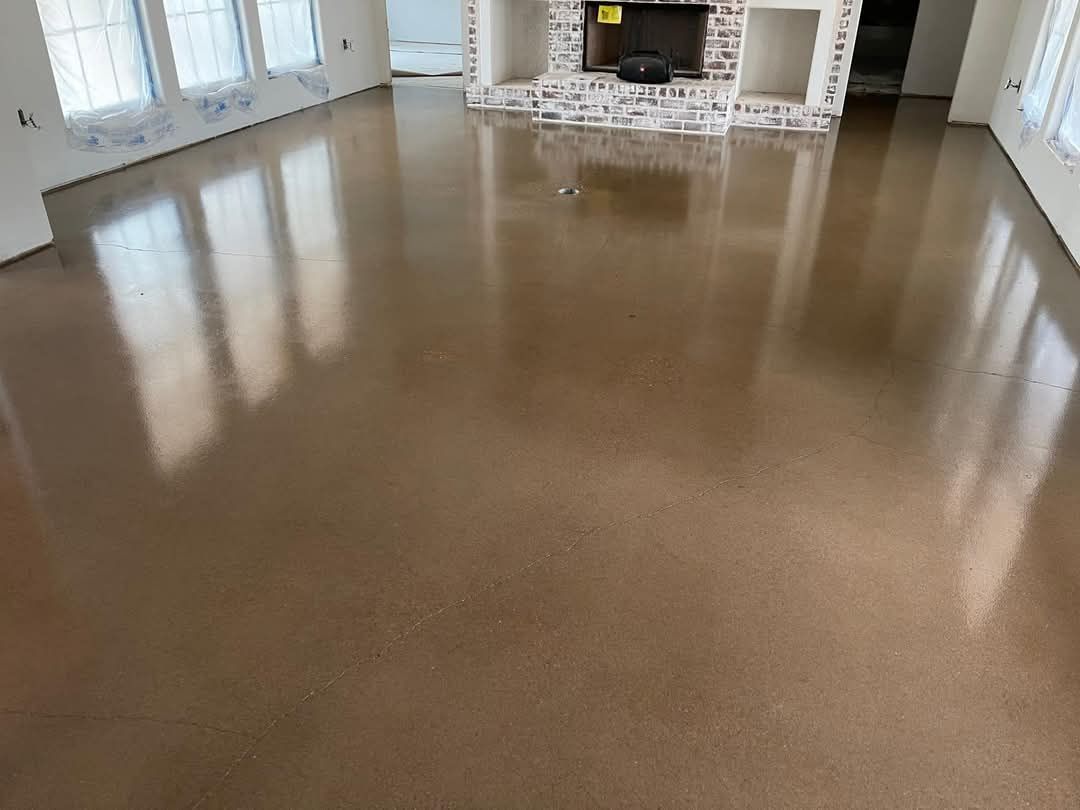
Different coating formulations offer varying levels of durability and life expectancy, making selection crucial for your specific floor application and environmental conditions.
Epoxy Floor Coatings
Epoxy coatings typically last 5-10 years on basement floors, garage surfaces, and warehouse applications when properly maintained. Their exceptional hardness and chemical resistance make them popular for concrete areas exposed to oil, grease, and mechanical wear. However, UV exposure from sunlight can reduce lifespan through etching and degradation. Regular maintenance helps maintain effectiveness against stains, abrasion, and moisture-related deterioration.
Polyurea Systems
Polyurea coatings demonstrate superior durability, lasting 7-15 years even under demanding conditions with heavy equipment and extreme pressure. Their flexibility and abrasion resistance contribute significantly to extended lifespan, making them excellent for concrete surfaces exposed to tire traffic, heat stress, and harsh climate conditions in warehouse and industrial environments.
Polyurethane Applications
Polyurethane coatings typically last 8-12 years, offering excellent protection against wear and tear while maintaining superior aesthetics. Their outstanding UV resistance makes them suitable for outdoor applications like patios, driveways, and decorative concrete surfaces exposed to sunlight and moisture while preserving waterproofing properties and visual appeal.
Decorative and Specialty Coatings
Decorative concrete coatings, including metallic epoxy and textured systems, offer similar durability to standard formulations while providing enhanced aesthetics for residential and commercial applications. These specialty coat systems may require more frequent maintenance in high-abrasion environments, but excel in preserving both functionality and visual appeal.
Coating Comparison Summary
This comprehensive comparison helps you understand key differences between coating types and their optimal applications based on durability and performance.
Coating Type | Average Lifespan | Key Characteristics | Ideal Application |
---|---|---|---|
Epoxy | 5–10 years | Hard finish, chemical resistant, oil resistant | Garage floors, basement surfaces |
Polyurea | 7–15 years | Fast curing, heat resistant, abrasion resistant | Warehouses, heavy equipment zones |
Polyurethane | 8–12 years | UV resistant, flexible, aesthetically appealing | Outdoor patios, decorative concrete |
Latex Systems | 3–7 years | Economical, easy application, moderate durability | Light-duty residential applications |
Extend Coating Life Through Maintenance
Implementing proper maintenance strategies significantly extends your coating's lifespan while preserving both appearance and functionality against environmental stress.
Regular cleaning with appropriate chemicals prevents buildup of dirt, dust, grease, and other contaminants that can compromise adhesion and cause staining. Early damage detection through systematic inspections and immediate spill cleanup prevent escalation of problems that could affect the floor's structural integrity. Apply touch-up coatings and seal cracks immediately to maintain waterproofing effectiveness and prevent moisture infiltration that leads to concrete deterioration.
Professional pressure washing removes embedded soil and contaminants while preserving the coating surface. Protective topcoats guard against micro-abrasions, etching, and chemical damage from oil, grease, and industrial chemicals. Address cracks, chips, or peeling immediately to prevent moisture infiltration and further deterioration that compromises adhesion and waterproofing capabilities.
Sealers create moisture barriers and reduce staining from oil and grease, while UV blockers minimize sun damage and prevent degradation from sunlight exposure. These protective products enhance durability and extend life expectancy by creating additional barriers against environmental stress and wear.
Environmental Impact on Coating Performance
Different environments present unique challenges that directly affect coating durability, requiring careful consideration of application-specific factors.
Residential Applications
Indoor environments like garages, basements, and decorative concrete surfaces typically allow coatings to last 5-10 years with controlled climate conditions and limited extreme weather exposure. However, tire traffic from vehicles, oil and grease spills, and cleaning chemicals still cause wear and tear requiring regular maintenance. Proper humidity control and ventilation help prevent moisture-related deterioration.
Commercial and Industrial Environments
Warehouse floors and industrial facilities subject coatings to heavy equipment, mechanical abrasion, chemical exposure, heat, and constant pressure, typically reducing lifespan to 5-8 years despite high-performance formulations. These demanding environments require specialized coat systems designed to withstand extreme conditions while maintaining adhesion and waterproofing properties under continuous stress.
Outdoor Applications
Outdoor coatings on patios, driveways, decks, and decorative concrete face rapid degradation from sunlight, precipitation, humidity variations, and environmental pollutants. Even with UV-resistant formulations and protective additives, outdoor applications typically last 4-8 years due to constant exposure to weather cycles, soil contamination, and thermal expansion. Regular sealing, pressure washing, and protective maintenance are essential for preventing moisture infiltration and preserving aesthetics.
Choose the Right Coating System
Selecting the optimal coating requires careful evaluation of your specific environment, usage patterns, and performance requirements for maximum longevity.
Evaluate traffic levels, climate conditions, budget constraints, and aesthetic requirements when selecting between epoxy, polyurea, and polyurethane systems. High-traffic warehouse applications benefit from polyurea's superior durability and resistance to heavy equipment and heat, while residential garage floors may find epoxy sufficient for typical wear patterns. For outdoor patios, driveways, or decorative concrete applications, polyurethane offers optimal balance between visual appeal, UV resistance, and long-term durability.
Consider initial installation costs against ongoing maintenance requirements, pressure washing frequency, and replacement schedules for accurate long-term value assessment. Factor in environmental conditions like humidity, temperature extremes, and exposure to oil, grease, and other contaminants that may affect coating performance and overall life expectancy.
Get Professional Concrete Coating Services
Ready to protect and enhance your concrete surfaces with premium coating solutions? Hero Concrete Coatings offers expert installation of epoxy, polyurea, and polyurethane systems designed to maximize durability and longevity for your specific application needs. Contact Hero Concrete Coatings today for a free consultation and discover how our professional-grade coating systems can transform your garage, basement, warehouse, or decorative concrete surfaces.
In Summary
Maximizing concrete coating performance requires careful planning, proper installation, and consistent maintenance practices tailored to your specific application.
Concrete coatings represent vital investments for floor protection and enhancement in basement, garage, warehouse, patio, deck, and driveway applications. Success depends on selecting appropriate epoxy, polyurea, or polyurethane products matched to specific environmental conditions and usage patterns. Professional installation ensures proper surface preparation, adhesion, and uniform coverage, while consistent maintenance, including pressure washing, prompt repairs, and protective treatments, maximizes durability against wear and tear, stains, moisture, and environmental stress for optimal longevity and performance.